Low-code для банка: автоматизация корпоративных продаж
Закрытая презентация нового решения ELMA365 Fintech и Nobilis.Team
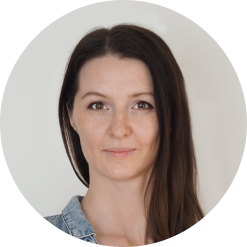
Мария Ильина
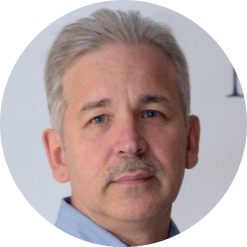
Андрей Кузин
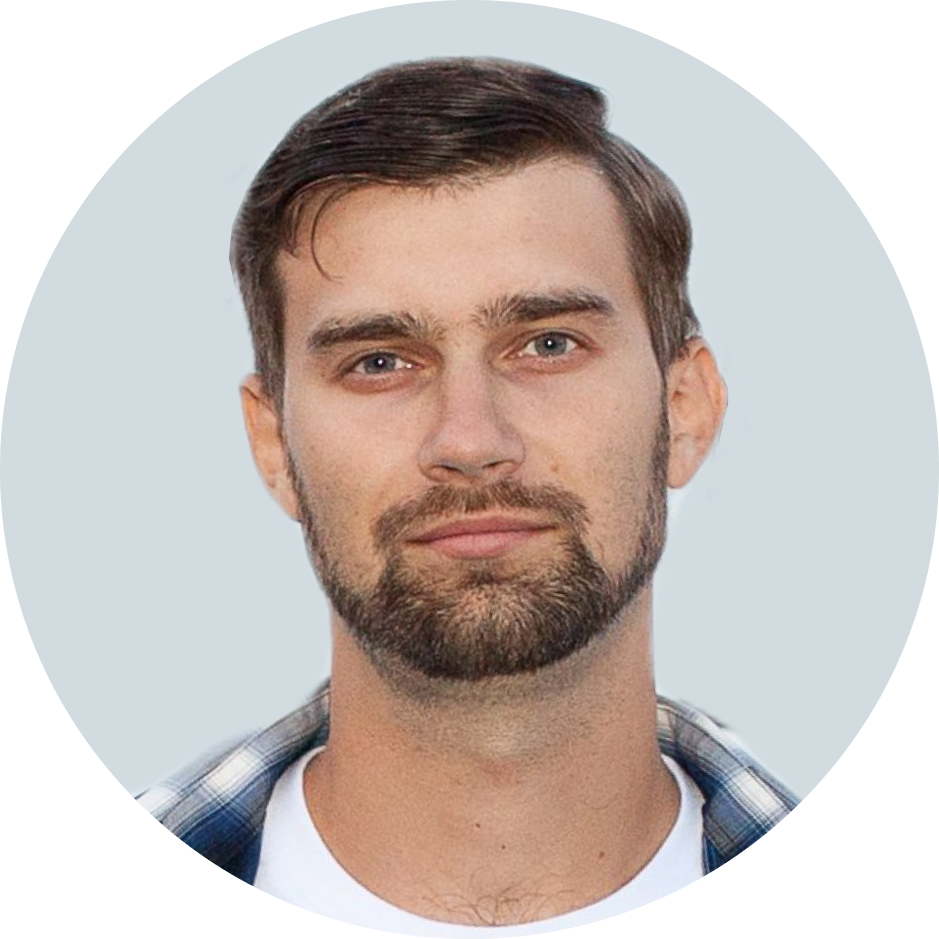
Александр Закамский
Создавайте корпоративные приложения быстрее и с меньшим количеством программного кода
Быстрая ECM-система, построенная на современных облачных технологиях
Самая внедряемая система управления бизнес-процессами (BPM) в СНГ
Графики проектов, управление ресурсами, бизнес-процессы в проектах
Единая платформа для автоматизации продаж и клиентского сервиса
Быстрые изменения невозможны без гибких ИТ, поэтому инструменты
цифровой трансформации не должны требовать серьезного
технического бэкграунда.
За счет низкого порога
входа Low-code инструментов бизнес-пользователи и аналитики
могут внедрять свои идеи и создавать собственные
бизнес-приложения. Это новая реальность, в которой
внедрение изменений занимает дни, а не месяцы.
Как крупная ИТ-компания нашла замену продуктам зарубежных вендоров на рынке российского ПО
Рассказываем про автоматизацию нового инвестиционного направления Банка Синара с помощью Low-code ELMA365 CRM
24 апреля в прямом эфире в формате видеоподкаста состоялась традиционная технологическая конференция ELMA Power UP!
«Татнефть – Цифровое развитие» внедрит сервисную платформу ELMA365 для замены Creatio.
ELMA проведет 24 апреля онлайн-конференцию на тему Low-code микросервисов, CX и CSP — ELMA Power UP!
Главная
«Современный мир ускоряется и дистанцируется. Компаниям необходимо быть быстрее и иметь актуальные сервисы. Цифры говорят, что после оцифровки мы можем делать тоже самое, что делали ранее, но с меньшим количеством ресурсов. BPMs создает потенциал хорошего, взрывного роста»
Владимир Лебедев,
руководитель проектов «Московского кредитного банка»